Comprehensive Guide to H2S Training: Ensuring Safety in the Workplace
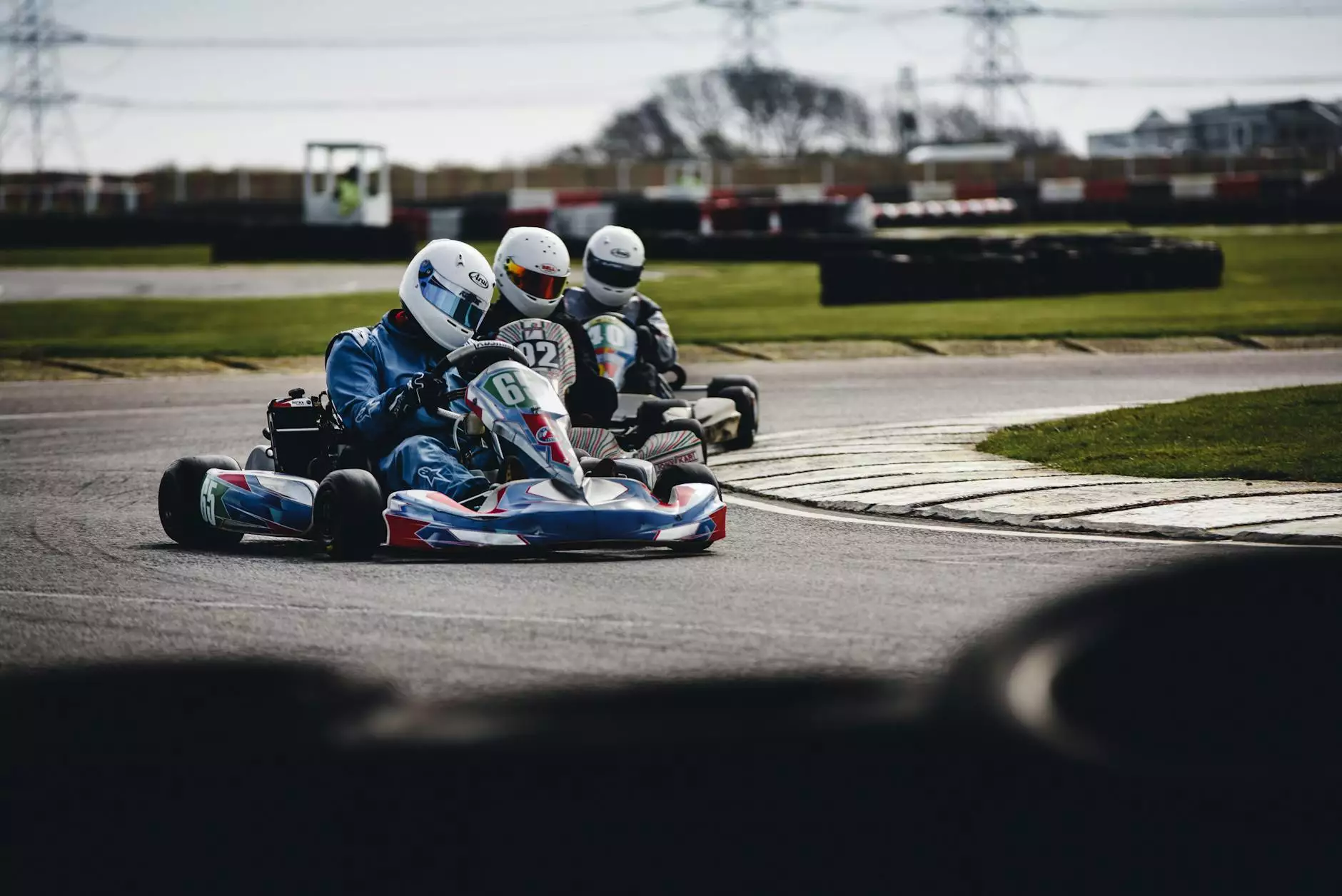
H2S training is an essential component of workplace safety in industries dealing with hazardous materials, particularly in the oil and gas, waste management, and petrochemical sectors. As awareness of workplace hazards increases, so does the need for effective training programs that prepare employees to recognize and respond to the dangers posed by hydrogen sulfide (H2S). This article delves into the importance of H2S training, its legal requirements, and best practices for implementing effective programs.
Understanding Hydrogen Sulfide (H2S)
Hydrogen sulfide (H2S) is a colorless gas known for its distinct odor of rotten eggs. It is highly toxic and can lead to serious health issues if not properly managed. Understanding the properties and risks associated with H2S is crucial for employees working in environments where this substance is present.
Properties of H2S
- Colorless and Odorless: H2S is nearly invisible and can be difficult to detect without proper equipment after high exposure.
- Toxicity: Exposure to hydrogen sulfide can lead to health complications, ranging from irritation of the eyes and throat to more severe health effects like respiratory failure.
- Flammability: H2S is flammable and can contribute to explosions in confined or poorly ventilated spaces.
The Importance of H2S Training
Implementing H2S training is critical for safeguarding the health and safety of employees. Here are the key reasons why effective training is indispensable:
1. Legal Compliance
Many regions have strict regulations concerning the handling and exposure to hazardous materials, including H2S. Compliance with these regulations, such as OSHA (Occupational Safety and Health Administration) standards in the United States, requires employers to provide appropriate training. Failure to adhere to these regulations can result in legal penalties and fines.
2. Health and Safety
Through H2S training, employees learn to understand the risks associated with hydrogen sulfide. This knowledge enables them to take proactive measures to protect themselves and their colleagues, significantly reducing the likelihood of accidents and injuries in the workplace.
3. Emergency Preparedness
Training programs prepare employees to act swiftly and decisively in the event of an H2S release or exposure. This includes identifying early signs of exposure, utilizing appropriate personal protective equipment (PPE), and executing emergency response protocols effectively.
4. Enhanced Workplace Culture
A commitment to safety through H2S training fosters a culture of awareness. When employees are educated and encouraged to discuss safety concerns, it leads to a more communicative and vigilant work environment.
Components of an Effective H2S Training Program
Creating a comprehensive H2S training program involves several key components. An effective program should encompass the following:
1. Training Curriculum
The training curriculum should cover:
- Properties of H2S: Understanding the physical and chemical properties of hydrogen sulfide.
- Health Hazards: Information on acute and chronic health effects of H2S exposure.
- Detection and Monitoring: Training on methods to detect H2S, including personal and area monitoring systems.
- Personal Protective Equipment (PPE): Guidelines for selecting and using the right PPE for different work scenarios.
- Emergency Procedures: Clear instructions on evacuation routes, first aid, and emergency response roles.
2. Hands-On Training
In addition to theoretical knowledge, hands-on training is essential. Practical demonstrations allow employees to operate detection equipment, wear PPE correctly, and engage in emergency drills, thus reinforcing their understanding through experience.
3. Assessment and Certification
To ensure that employees fully grasp the material, assessments should be conducted at the end of the training. Providing certification upon successful completion not only validates their knowledge but also serves as a tangible reminder of their commitment to safety.
Legal Requirements for H2S Training
Understanding the legal landscape surrounding H2S training is crucial for organizations. Various standards, such as those set by OSHA, dictate the necessary training protocols. Here are some important points to consider:
1. OSHA Standards
OSHA 1910.1000 outlines the permissible exposure limits for H2S and emphasizes the necessity of proper training and protective measures. Employers must ensure their workforce is trained adequately on the hazards and safe practices concerning H2S.
2. State Regulations
In addition to federal regulations, many states have their own laws concerning H2S handling and training. Companies should stay informed about local legal requirements to ensure full compliance.
Best Practices for Implementing H2S Training
To maximize the effectiveness of your H2S training program, consider the following best practices:
1. Regular Training Updates
H2S training should not be a one-time event. Regular updates are crucial to account for any new regulations, advancements in technology, or changes in workplace procedures.
2. Tailored Programs
Different roles within an organization may have varying exposure to H2S. Tailoring training programs to specific job functions ensures that employees receive relevant and applicable information.
3. Feedback Mechanisms
Establishing a feedback loop allows employees to voice their concerns or suggestions regarding the training program. This engagement helps improve training quality and effectiveness over time.
4. Utilization of Technology
Leverage technology, such as online training modules and virtual reality simulations, to enhance the learning experience. These tools can provide an engaging and interactive approach to H2S training.
Conclusion
In conclusion, H2S training is an essential aspect of workplace safety for organizations operating in environments where hydrogen sulfide may be present. By investing in comprehensive training programs, businesses not only comply with legal regulations but also prioritize the health and safety of their employees. Through continuous education, hands-on practice, and a commitment to fostering a safety-centric culture, companies can significantly reduce the risks associated with H2S exposure. Remember, safety is not just a priority; it is a value that drives the success of any organization.
Call to Action
If you are looking to enhance your H2S training program or need to develop a new training initiative, consider contacting h2sonlinetraining.com for expert guidance and comprehensive training solutions tailored to your needs.