Maximizing Efficiency with Electric Molding Techniques in Metal Fabrication
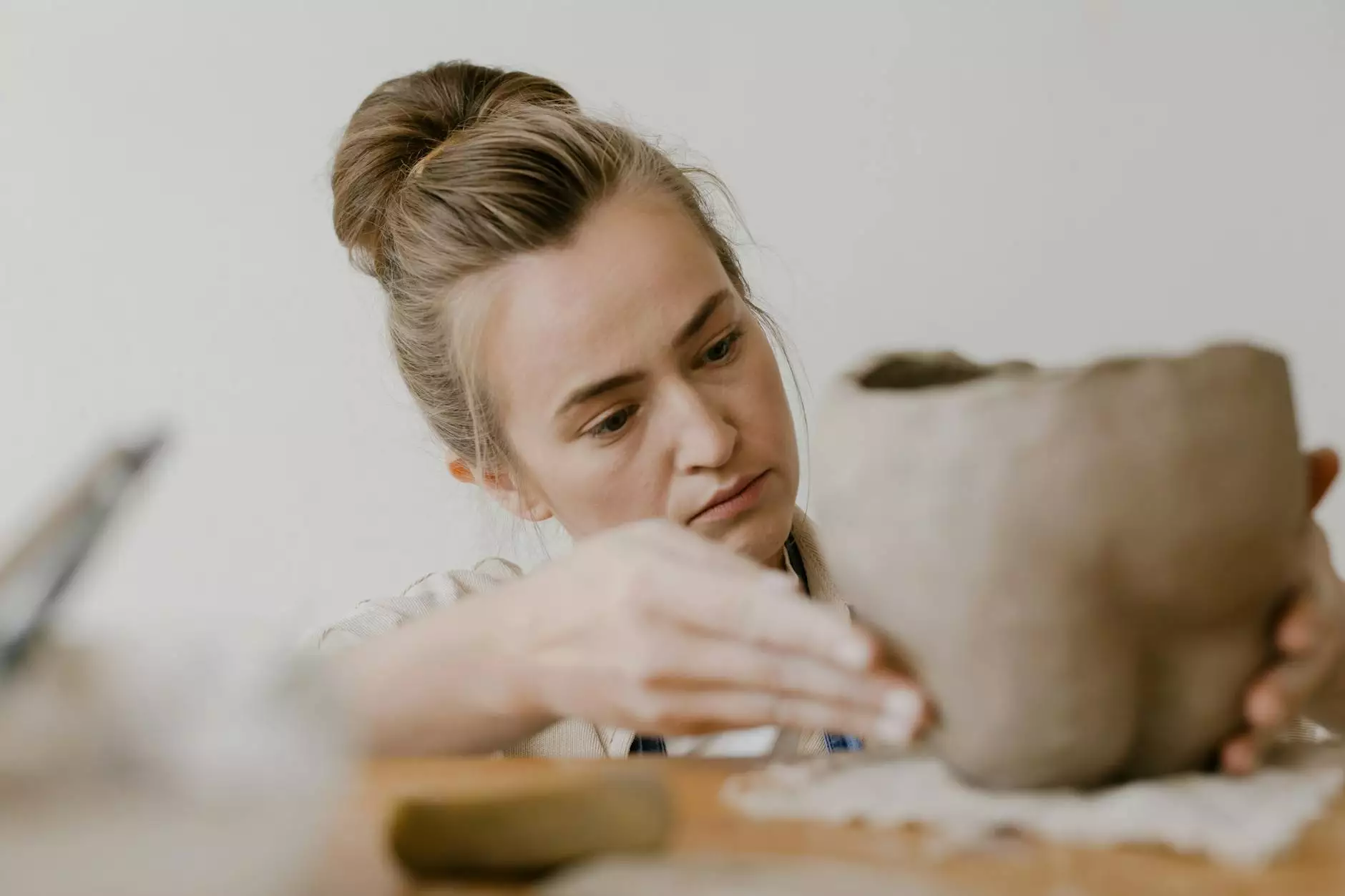
In the modern marketplace, businesses are constantly seeking ways to enhance efficiency, precision, and sustainability. One such revolutionary technique that has emerged within the metal fabrication industry is electric molding. This article delves deep into the intricacies of electric molding, its benefits, and how it can transform your fabrication processes. For businesses seeking to lead in innovation, utilizing electric molding can be a game-changer.
Understanding Electric Molding
Electric molding refers to a manufacturing process where electrical energy is employed to melt and mold materials, primarily metals and plastics, into precisely shaped products. It combines advanced technologies with traditional molding techniques to achieve superior outcomes in various applications. The rise of electric molding is partly driven by the increasing demand for efficiency and sustainability in manufacturing processes.
Benefits of Electric Molding in Metal Fabrication
Here are some of the key advantages that electric molding brings to the table for metal fabricators:
- Increased Precision: Electric molding techniques are renowned for their ability to produce parts with high accuracy and minimal tolerances. This precision is crucial in applications requiring exact specifications.
- Energy Efficiency: Electric molding systems consume significantly less energy compared to traditional hydraulic systems. This reduction not only lowers production costs but also contributes to a smaller carbon footprint.
- Improved Cycle Times: Due to the fast heating capabilities of electric systems, cycle times can be significantly reduced, leading to increased productivity.
- Enhanced Material Utilization: The precision of electric molding minimizes waste, allowing for better utilization of raw materials and cost savings.
- Greater Flexibility: Electric molding technology allows for quick adjustments and changes in production runs, accommodating custom jobs and varying customer demands more easily.
- Lower Maintenance Costs: Electric systems generally have fewer moving parts than hydraulic systems, which translates to lower maintenance and repair costs over time.
The Process of Electric Molding
The process of electric molding involves several key steps:
1. Material Preparation
The first step in the electric molding process is the sourcing and preparation of materials. Metals such as aluminum, copper, and steel are commonly used, depending on the desired properties of the final product. These materials are cleaned and sometimes pre-heated to ensure optimal performance during molding.
2. Melting
Electric molding utilizes induction heaters or electric resistance systems to melt the metal. This melting process is highly controlled, allowing for precise temperature management which is critical for achieving the desired metallurgical properties.
3. Injection and Molding
Once the material is melted, it is injected into pre-formed molds. These molds can be designed with high precision to meet specific requirements. The ability to heat both the mold and the material can significantly improve the quality of the finished part.
4. Cooling and Solidification
After injection, the material is allowed to cool and solidify into the desired shape. The cooling process can be optimized using various techniques to ensure consistent quality across production runs.
5. Finishing
The last step involves finishing processes such as machining, coating, or painting to enhance the product's durability and appearance. Finishing is essential for achieving the required surface finish and dimensional tolerances.
Applications of Electric Molding
The versatility of electric molding makes it applicable in various industries, notably:
- Aerospace: High-precision components for aircraft manufacturing.
- Automotive: Production of intricate parts that require tight tolerances.
- Consumer Electronics: Manufacturing components that demand high efficiency and low power consumption.
- Medical Devices: Production of sterile, precise components critical to medical technology.
Choosing the Right Electric Molding Partner
When considering the transition to electric molding, it is essential to partner with experienced and reputable metal fabricators. Here are some factors to consider when choosing the right partner:
- Experience: Look for a provider with extensive experience in electric molding and a proven track record of successful projects.
- Technology: Ensure that the company utilizes the latest technologies to provide high-quality products.
- Certifications: Verify that the fabricator meets industry standards and holds relevant certifications.
- Customization: Choose a partner that offers customizable solutions tailored to your specific needs.
- Customer Service: Evaluate their customer service and support, ensuring they prioritize client satisfaction.
Future Trends in Electric Molding
The future of electric molding looks promising, with several trends anticipated to shape its evolution:
- Smart Manufacturing: The integration of IoT technology will enable real-time monitoring and optimization of molding processes.
- Sustainability Initiatives: As sustainability continues to gain importance, electric molding will increasingly focus on reducing waste and energy consumption.
- Advanced Materials: The exploration of new materials that can be molded using electric techniques will expand the possibilities of this technology.
- Customization and 3D Printing: The convergence of electric molding and 3D printing will enable more intricate designs and customizations.
Conclusion
In conclusion, electric molding is not only a transformative technique within the metal fabrication industry but also a vital asset for businesses looking to innovate and excel. By embracing this advanced manufacturing process, companies can achieve unprecedented levels of efficiency, precision, and sustainability.
As you consider the future of your manufacturing practices, reflecting on the benefits and implementations of electric molding may provide you with the strategic advantage needed to thrive in the competitive landscape. For expertise and excellence in electric molding and more, explore partnerships with leaders in the field such as Deep Mould. Your journey towards improved production efficiency and product quality begins here.