Unlocking the Potential of 3D Printing with PBF Technology
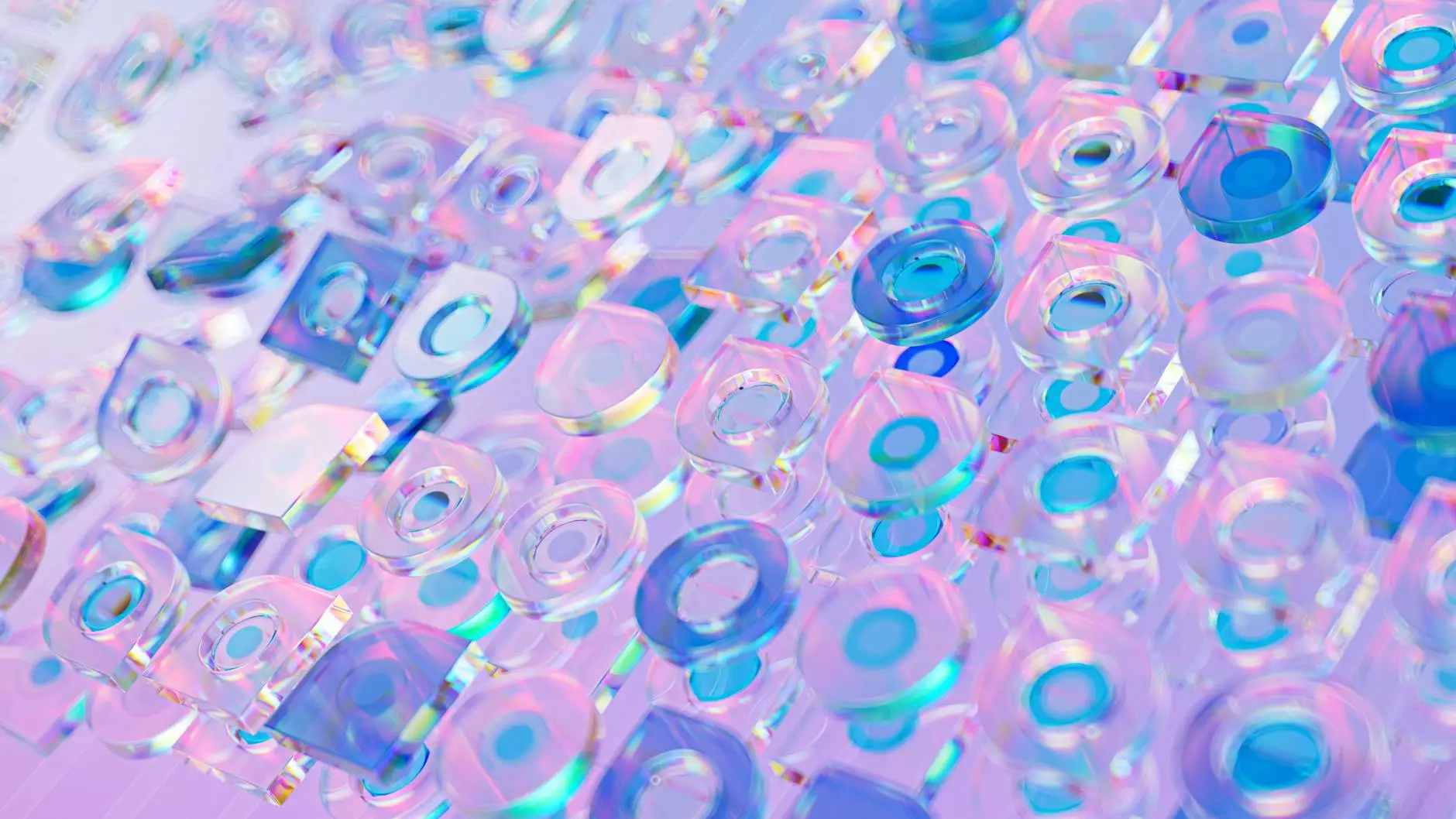
In recent years, the landscape of manufacturing and product development has been transformed by advances in 3D printing technology. Among the most groundbreaking innovations in this field is Powder Bed Fusion (PBF), a versatile and highly precise additive manufacturing process that is redefining what is possible in industrial production. At Infotron, we are dedicated to leveraging the latest in 3D printing technology, including PBF, to help businesses innovate, optimize, and lead in their respective markets.
What is Powder Bed Fusion (PBF) in 3D Printing?
Powder Bed Fusion (PBF) is an advanced additive manufacturing process that builds parts layer by layer by selectively fusing powder materials using thermal energy sources such as lasers or electron beams. This technique is distinguished by its ability to produce high-resolution, complex geometries that are often impossible to achieve with traditional manufacturing methods.
In PBF, a thin layer of powder is spread across a build platform. The energy source then selectively fuses microscopic particles of powder according to the digital 3D model. After fusing one layer, the process repeats—repeating the cycle until the entire part is completed. The un-fused powder supports the part during building, eliminating the need for additional supports and reducing post-processing time.
The Core Principles and Process of PBF
Step-by-Step Overview of PBF Manufacturing
- Preparation: The digital model of the part is sliced into thin layers using specialized software. The machine's parameters are set based on material properties and desired final qualities.
- Powder Spreading: A thin, even layer of powder is spread across the build platform using a roller or blade.
- Selective Fusing: The energy source, such as a laser or electron beam, scans across the powder bed, fusing particles together according to the sliced layer data.
- Layer Lowering: The build platform lowers by one layer thickness, and a new powder layer is spread for the next cycle.
- Repeat: The process repeats—layer by layer—until the complete component is formed.
- Cooling and Post-Processing: The part is cooled gradually to prevent warping. Post-processing steps such as cleaning, heat treatment, and surface finishing enhance the final quality.
Advantages of PBF in 3D Printing
- High Precision and Detail: PBF technology offers exceptional resolution, allowing for the creation of complex geometries with intricate details that outperform traditional manufacturing methods.
- Design Flexibility: The layer-by-layer approach enables rapid prototyping and customization, making it ideal for bespoke parts or small production runs.
- Material Versatility: PBF can process a wide range of materials, including metals like titanium, aluminum, stainless steel, nickel alloys, and specialized polymers, expanding application possibilities.
- Reduced Waste: Since parts are built directly from digital models, material waste is minimized—only the required amount of powder is used, supporting sustainability objectives.
- Strong Mechanical Properties: Parts produced via PBF exhibit excellent strength, durability, and surface finish—suitable for critical engineering applications.
- Rapid Production Cycles: Compared to traditional manufacturing, PBF accelerates the development cycle from design to final part, enabling faster time-to-market.
Economical and Strategic Benefits for Your Business with PBF
Implementing PBF technology in your business offers numerous strategic advantages:
- Cost Savings: While initial equipment costs can be significant, the reduction in tooling, assembly, and post-processing reduces overall production expenses.
- On-Demand Manufacturing: Produce parts as needed, avoiding inventory costs and allowing for flexible, just-in-time production strategies.
- Innovation and Customization: Rapidly iterate designs to optimize performance, aesthetics, and functionality, gaining a competitive edge.
- Supply Chain Resilience: In-house production capabilities reduce dependence on external suppliers and mitigate supply chain disruptions.
- Access to New Markets: PBF enables the manufacturing of lightweight, complex parts suitable for aerospace, automotive, medical, and jewelry industries—opening new revenue streams.
Key Industries Benefiting from PBF Technology
1. Aerospace and Defense
High-performance components with complex geometries, lightweight structures, and superior strength are essential in aerospace applications. PBF allows for the production of aerospace-grade parts such as engine components, structural elements, and customized tools with minimal weight and optimized durability.
2. Medical and Dental
Customized implants, surgical guides, and dental prosthetics are revolutionized through PBF's ability to produce highly personalized, intricate devices that fit patients precisely, improving outcomes and reducing surgery times.
3. Automotive
From lightweight brackets to performance-enhancing parts, automotive manufacturers leverage PBF to accelerate innovation and reduce part weight, leading to better fuel efficiency and vehicle performance.
4. Jewelry and Fashion
Designers utilize PBF to craft intricate, bespoke jewelry pieces with complex patterns and fine details, expanding creative possibilities while reducing production times.
5. Tooling and Manufacturing Aids
Custom jigs, fixtures, and molds can be rapidly created with PBF, improving manufacturing efficiency and enabling rapid tooling development.
Future Trends and Innovations in PBF Technology
The landscape of PBF and 3D printing is continually evolving. Emerging trends include:
- Multi-Material Printing: Advances will enable the fabrication of parts with multiple materials in a single build, adding functionality such as embedded electronics or gradient properties.
- Automation and AI Integration: Combining PBF with automation and machine learning will streamline production, improve quality control, and reduce human intervention.
- Materials Development: New alloys and polymers specifically designed for PBF will enhance mechanical properties, biocompatibility, and surface finish.
- Large-Scale and Modular Systems: Expanding build volume and modular machine designs will accommodate industrial-scale production and complex assembly processes.
- Sustainable Practices: Recycling unused powder, energy-efficient lasers, and environmentally friendly materials will make PBF a greener manufacturing option.
As these innovations unfold, Infotron remains at the forefront, integrating the latest PBF solutions to meet diverse industry needs and drive sustainable growth.
Why Choose Infotron for Your PBF and 3D Printing Needs?
At Infotron, we specialize in providing cutting-edge 3D printing solutions, including PBF, tailored to your specific requirements. Our team of experts offers:
- Comprehensive Consultation: Assisting in selecting the right materials and process parameters for your project.
- State-of-the-Art Equipment: Access to the latest PBF machinery for high-precision, reliable production.
- Material Expertise: Extensive knowledge of diverse powders, ensuring optimal results and material properties.
- Quality Assurance: Rigorous testing, inspection, and certification processes to guarantee high standards.
- Prototyping to Production: End-to-end services from initial design validation to full-scale manufacturing.
Partnering with Infotron empowers your business to harness the full potential of PBF technology, building innovative products that excel in today's competitive markets.
Transform Your Business with PBF-Driven 3D Printing Today
Understanding and integrating PBF into your manufacturing and product development strategies can significantly enhance your capabilities and market positioning. The precision, flexibility, and efficiency offered by this technology open a world of possibilities for diverse sectors. Whether you're looking to develop complex aerospace components, customized medical devices, or innovative consumer products, 3D printing with PBF is your key to staying ahead.
At Infotron, we are committed to guiding you through this technological evolution, ensuring quality, innovation, and success every step of the way.